Extracting Key Data from Hitachi ZX350LC-6
Integrate your Hitachi ZX350LC-6 with AutoPi CAN-FD Pro
Comprehensive J1939 CAN Bus Logging – Capture all machine signals and parameters for detailed analysis.
Predictive Maintenance – Use historical data to predict failures and schedule repairs before breakdowns occur.
Fuel Optimization – Analyze fuel injection data and consumption rates to reduce operating costs.
Hydraulic System Monitoring – Detect pressure inconsistencies and potential leaks in real time.
Fleet Utilization Analytics – Process J1939 CAN bus logs to improve scheduling and fleet-wide efficiency.
Remote Diagnostics – Access full CAN bus logs remotely to troubleshoot issues before dispatching service teams.
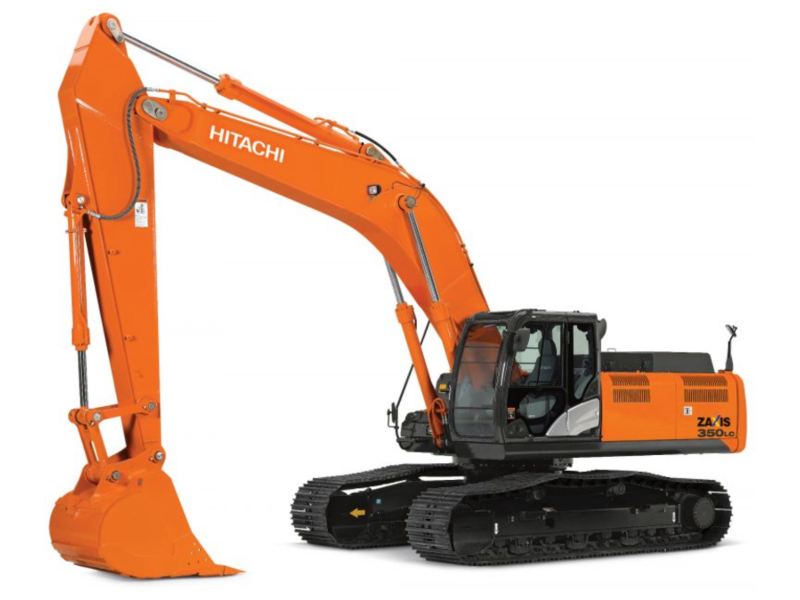
Extracting Key Data from Hitachi ZX350LC-6
The Hitachi ZX350LC-6 is a powerful, heavy-duty excavator designed for demanding earth-moving applications. Equipped with a 271 HP Isuzu engine, this machine offers exceptional performance for excavation, demolition, and material handling. The ZX350LC-6 has an operating weight of 35,800 kg, a digging depth of 7.38 meters, and an impressive breakout force of 246 kN, making it a top choice for contractors requiring high power and efficiency.
This model features Hitachi’s TRIAS II hydraulic system, which enhances fuel efficiency and reduces hydraulic power loss. Additionally, the reinforced boom and arm design ensure durability in extreme working conditions. However, without real-time data extraction, it can be challenging for fleet managers to optimize performance, reduce downtime, and enhance fuel efficiency.
Why AutoPi CAN-FD Pro?
AutoPi CAN-FD Pro integrates seamlessly with the Hitachi ZX350LC-6, enabling real-time logging of full CAN bus data, including engine health, hydraulic system performance, fuel consumption, and component wear. With CAN-FD and J1939 protocol support, AutoPi ensures high-speed, precise data transmission, allowing fleet operators to gain deeper insights into machine utilization and maintenance needs.
With full J1939 CAN bus logging, AutoPi CAN-FD Pro continuously captures and stores all relevant machine parameters, including engine RPM, fuel rate, hydraulic pressure, coolant temperature, and load percentage. This data can be securely uploaded to Amazon S3, ensuring a long-term historical record of the excavator's performance. By leveraging Databricks, operators can process this data with AI and machine learning models, identifying performance trends, optimizing fuel usage, and predicting component failures before they occur.
Key Specifications of AutoPi CAN-FD Pro
CAN-FD and J1939 Protocol Compatibility – Logs full J1939 CAN bus data from heavy equipment.
4G/LTE Connectivity – Enables remote access to real-time operational data.
Continuous J1939 Data Logging – Captures and stores CAN bus data for deep analysis.
AWS S3 Cloud Storage – Provides long-term storage of machine data.
Databricks AI Integration – Uses machine learning for predictive diagnostics and performance enhancement.
Rugged Industrial Design – Designed to withstand extreme worksite conditions.
By integrating AutoPi CAN-FD Pro with the Hitachi ZX350LC-6, operators gain unparalleled logging capabilities for machine performance analysis. The ability to upload full J1939 CAN bus data to AWS S3 and analyze it with Databricks AI enables deep insights into machine operations, predictive maintenance, and optimized fuel efficiency. This powerful combination allows fleet managers to maximize operational uptime, minimize costs, and ensure long-term machine reliability through comprehensive data-driven decision-making.
AutoPi CAN-FD Pro
Pro-specifications in a compact device
The AutoPi CAN-FD Pro is based on the Compute Module 4 from Raspbery Pi. The device is open and the AutoPi Core OS running on the device is open source. You can VPN/Tailscale into the device, making this the most versitile CAN bus data logger on the market.
Order now
In stock | Order now -> Ships tomorrow.
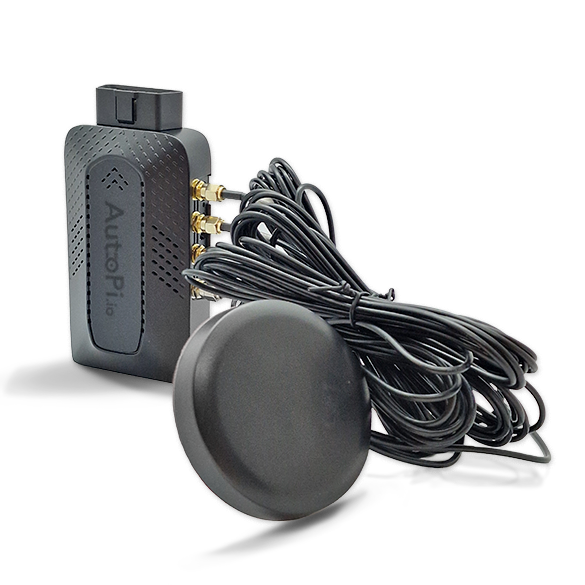
Comes with 4-in-1 external antenna for 2x 4G/LTE, 1x GPS and 1x WiFi/BLE.
More memory and more storage with options for external storage.
Shipped with our latest AutoPi Core OS, designed for high speed data logging.
Processor
Broadcom BCM2711 Quad-core Cortex-A72 (ARM v8) 64-bit SoC @ 1.5GHz (RPi CM4)
Memory
4GB LPDDR4 SDRAM
Storage
32GB on board eMMC (expandable with USB flash drive)
Modem
Integrated 4G/LTE Cat 4 connection (3G/EDGE fallback) (150Mbit DL / 50Mbit UL) (Global connectivity in a single device)
Secure Element
Sign and encrypt data
GPS/GNSS
Integrated GPS + A-GPS (GPS/GLONASS/BeiDou/Galileo/QZSS)
Power
Line Voltage: 12.5V DC (Car battery power). Up to 35V (Trucks). Support for trucks with up to 35V
Expansion
2 x USB, Gigabit Ethernet and HAT
Wireless
Bluetooth: Bluetooth 5.0 + Bluetooth Low Energy (BLE)
WiFi: 2.4GHz and 5GHz IEEE 802.11.b/g/n/ac wireless LAN
Accelerometer
3-Axis accelerometer
Gyroscope
Built in 3-axis gyroscope
Automotive Interface
2X CAN-FD interface with up to 5Mbps Data rate with integrated CAN data filters
Input Slots
SIM Card: Nano SIM - (SIM subscription purchased separately)
Audio
Built-in speakers
Video Out
mini HDMI @ 1080p60 Video Output
Operating System
Raspbian OS with preconfigured AutoPi Core software